
Gear and Lobe Pumps
Gear Pumps
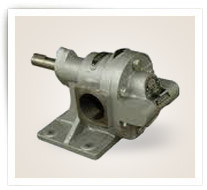
range
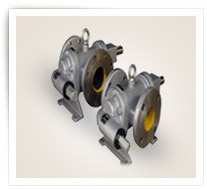
All pumps are self priming upto 5 mts.
Features of Standard Pumps
- Single Helical Gears
- Hardened & Ground Shafts
- Max Pressure - 10 kg/cm2
- Max Temperature - 80� C
PUMP FEATURES for special and rugged applications
- Heavy duty gear pump design for continuous application
- Double Herring bone rotor design eliminate side thrust
- Modified tooth profile enhances tooth life.
- Floating gear-design ensures uniform load distribution.
- Low-leakage path by design improve volumetric efficiency.
- Shorter bearing span reduces bending effect
- Max temp. 125� C
- Various different lubrication methods.
- Optional sealing arrangements
- Continuous duty
- Maximum pressure upto 20 bars/20 Kg per cm2.
- Stainless steel gear pumps for special applications.
- Special Designs for Ship�s fire pumps, FIFI 1, FIFI 2, FIFI 3, etc.
- With Gear Box or Direct Coupled.
- Flange mounted, or base mounted.
- Coupled or gear box or pulley driven.
Prime movers
Electric Motor/ Diesel Engine/ Petrol Engine.
Applications
- Steel plants
- Cement plants
- Petroleum industries
- Refineries
- Loading and unloading of tankers
- Petrochemicals
- Petrol
- Diesel
- Fuel oil
- Furnace oil
- Lube oil
- Viscous Liquids
- Process Industries
- Petrochemicals
- Wide Range of Viscous Liquids
- Fire Fighting
- Corrosive And Abrasive Liquids
- Lube oil transfer
- Fuel oil transfer
- Shipping and offshore
Internal Gear Pumps
Fuel Pressuring internal gear Pump Internal gear pumps are exceptionally versatile. While they are often used on thin liquids such as solvents and fuel oil, they excel at efficiently pumping thick liquids such as asphalt, chocolate, and adhesives. The useful viscosity range of an internal gear pump is from 1cPs toover1,000,000cP.
In addition to their wide viscosity range, the pump has a wide temperature range as well, handling liquids up to 750�F / 400�C. This is due to the single point of end clearance (the distance between the ends of the rotor gear teeth and the head of the pump). This clearance is adjustable to accommodate high temperature, maximize efficiency for handling high viscosity liquids, and to accommodate for wear.
Range
All pumps are self priming upto 5 mts.
Features
- Higher suction lift
- Self priming and capacity to create vacuum up to 600/650 mm hg
- Flange & Foot mounting option
- In built relief valve
- External by-pass arrangement
- Zero leakage Mechanical Seal
- Continues duty pump
Application (Internal Gear Pumps)
- Fuel injection in burners, boilers, furnaces
- Booster application in diesel locomotive
- Force feed lubrication
- Heating system.
Rotary Lobe Pumps
Rotary lobe pumps use timing gears to eliminate contact between the rotors, which allows their use on non-lubricating fluids. These pumps offer low shear and gentle handling of the liquid to minimize product degradation. Rotrary lobe pumps are useful for pumping and Transfer of all high viscous liquids like syrup paints, drugs, food products, etc. Rotary Lobe pumps are used in a variety of industries including, pulp and paper, chemical, food, beverage, pharmaceutical, and biotechnology. They are popular in these diverse industries because they offer superb sanitary qualities, high efficiency, reliability, corrosion resistance, and good clean-in-place and sterilize-in-place (CIP/SIP) characteristics.
Range
All pumps are self priming upto 5 mts.
Features (Rotary Lobe Pumps)
- Robust construction
- Compact size
- High efficiency
- Reversible operation
- Hygienic design
- Easy maintenance
- Inter changeable rotor
- Handling low as well as high viscous liquid
- Ideal for delicate media & where organic solid suspended particle in liquid
Working for Lobe Pump
Lobe pumps are similar to external gear pumps in operation in that fluid flows around the interior of the casing. Unlike external gear pumps, however, the lobes do not make contact. Lobe contact is prevented by external timing gears located in the gearbox. Pump shaft support bearings are located in the gearbox, and since the bearings are out of the pumped liquid, pressure is limited by bearing location and shaft deflection.
- As the lobes come out of mesh, they create expanding volume on the inlet side of the pump. Liquid flows into the cavity and is trapped by the lobes as they rotate.
- Liquid travels around the interior of the casing in the pockets between the lobes and the casing -- it does not pass between the lobes.
- Finally, the meshing of the lobes forces liquid through the outlet port under pressure.
Lobe pumps are frequently used in food applications because they handle solids without damaging the product. Particle size pumped can be much larger in lobe pumps than in other PD types. Since the lobes do not make contact, and clearances are not as close as in other PD pumps, this design handles low viscosity liquids with diminished performance. Loading characteristics are not as good as other designs, and suction ability is low. High-viscosity liquids require reduced speeds to achieve satisfactory performance. Reductions of 25% of rated speed and lower are common with high-viscosity liquids.
Application (Rotary Lobe Pumps)
- Food industries
- Chemical industries
- Pharmaceutical industries
- Dairy industries
- Petrochemical industries
- Sewage plant